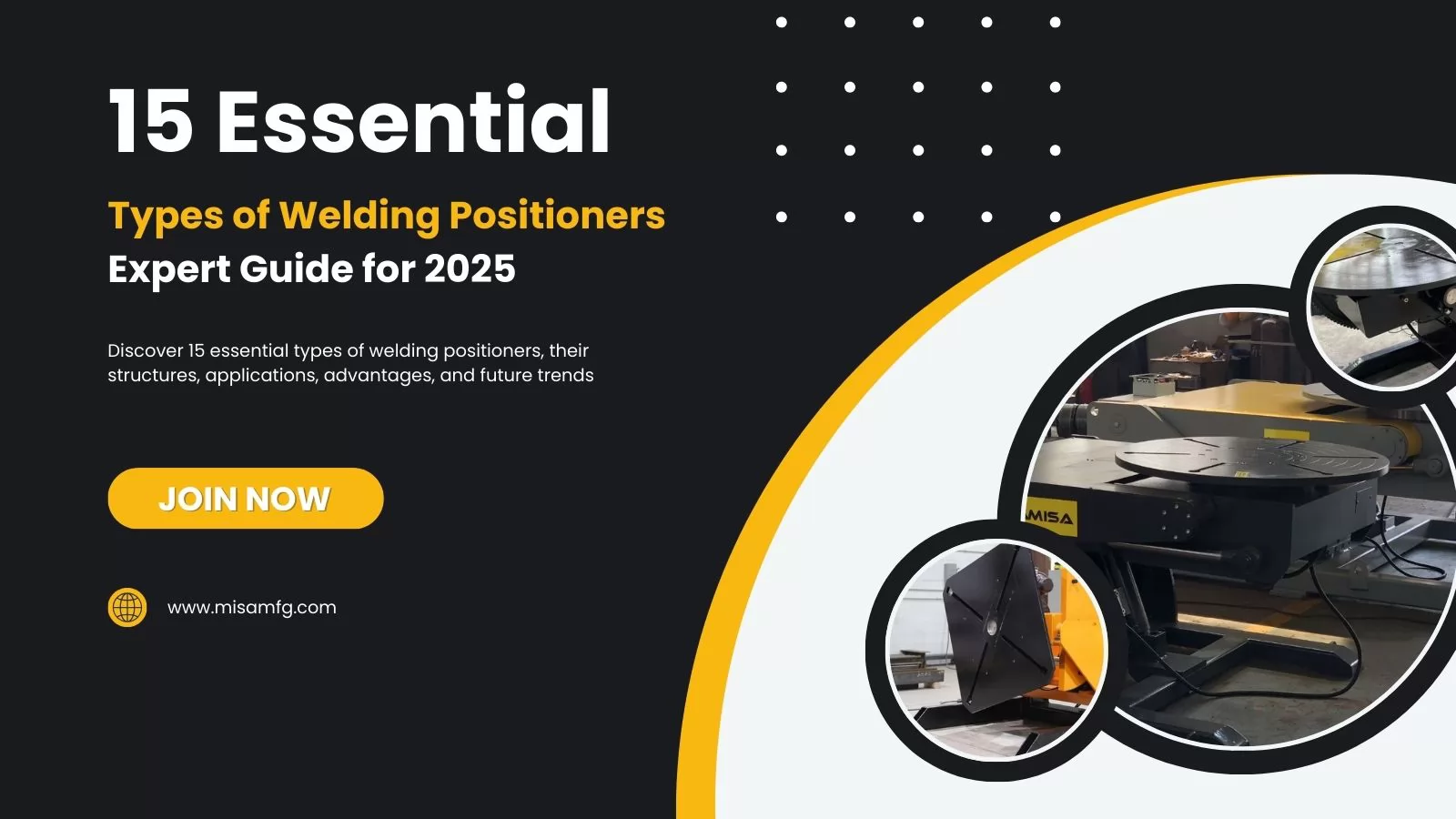
Table of Content
What is a Welding Positioner?
A welding positioner is a mechanical device engineered to rotate and tilt a workpiece, ensuring that the welder can perform operations in the most efficient and ergonomic position. This equipment supports the workpiece and moves it precisely, making complex welding jobs much easier and safer. By positioning the welding seam into a flat or horizontal position, the welding process becomes more consistent, resulting in higher-quality welds.
Importance of Using Welding Positioners
Welding positioners are crucial for projects involving round, cylindrical, or irregular components. Their use significantly reduces welder fatigue, improves productivity, and minimizes welding defects. As industries push for higher accuracy and safety standards, the demand for automation and support equipment like positioners is rapidly growing.
Key Benefits for Welders and Fabricators
-
Improved Weld Quality: Allows for better weld penetration and consistency.
-
Reduced Work Fatigue: Eliminates the need for awkward physical positions.
-
Time Efficiency: Speeds up the welding process by simplifying positioning.
-
Safety Enhancements: Keeps heavy workpieces stable during welding.
-
Automation Compatibility: Easily integrates with robotic welding arms and CNC controllers.
Rotational Mechanism
The core of a welding positioner is its rotating table or chuck that holds and spins the workpiece. Precision control of this rotation allows for uniform weld beads and reduced manual intervention.
Tilting Mechanism
This mechanism tilts the work platform at various angles, allowing access to otherwise hard-to-reach welding areas. Tilting is often powered by hydraulic or electric motors.
Control Systems and Automation
Modern positioners come with advanced control panels, including digital displays and programmable logic controllers (PLC), which enable precise movements, speed adjustments, and integration with robotic systems
Rotating Welding Positioners
Designed to spin the workpiece horizontally, these are ideal for circumferential welding tasks like pipes and cylinders.
Tilting Welding Positioners
These positioners can tilt the workpiece vertically, providing better access for welders and enhancing welding accuracy.
Elevating Welding Positioners
Capable of raising or lowering the work platform, they offer better ergonomics and flexibility in weld positioning—especially useful in large-scale fabrication.
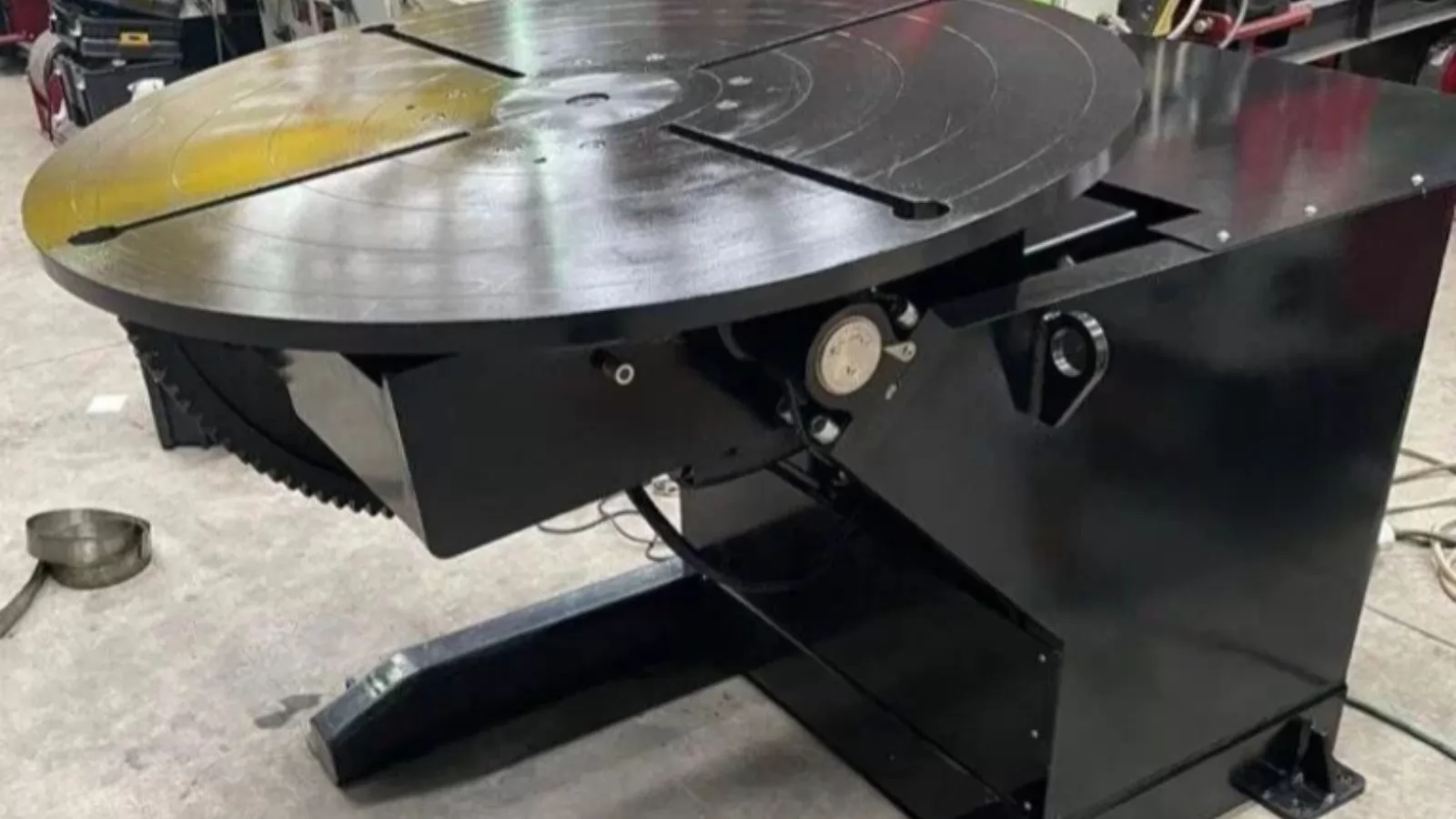
-
Structure: These positioners offer two degrees of freedom—rotation along the horizontal axis and tilt along the vertical axis.
-
Best For: Small to medium-sized components such as flanges, pipe fittings, and brackets.
-
Advantages: Simple design, cost-effective, and versatile for most general welding jobs.
-
Limitations: No vertical lift capability; limited support for large or irregular workpieces.
-
Industries Used: General fabrication, maintenance workshops, machinery manufacturing.
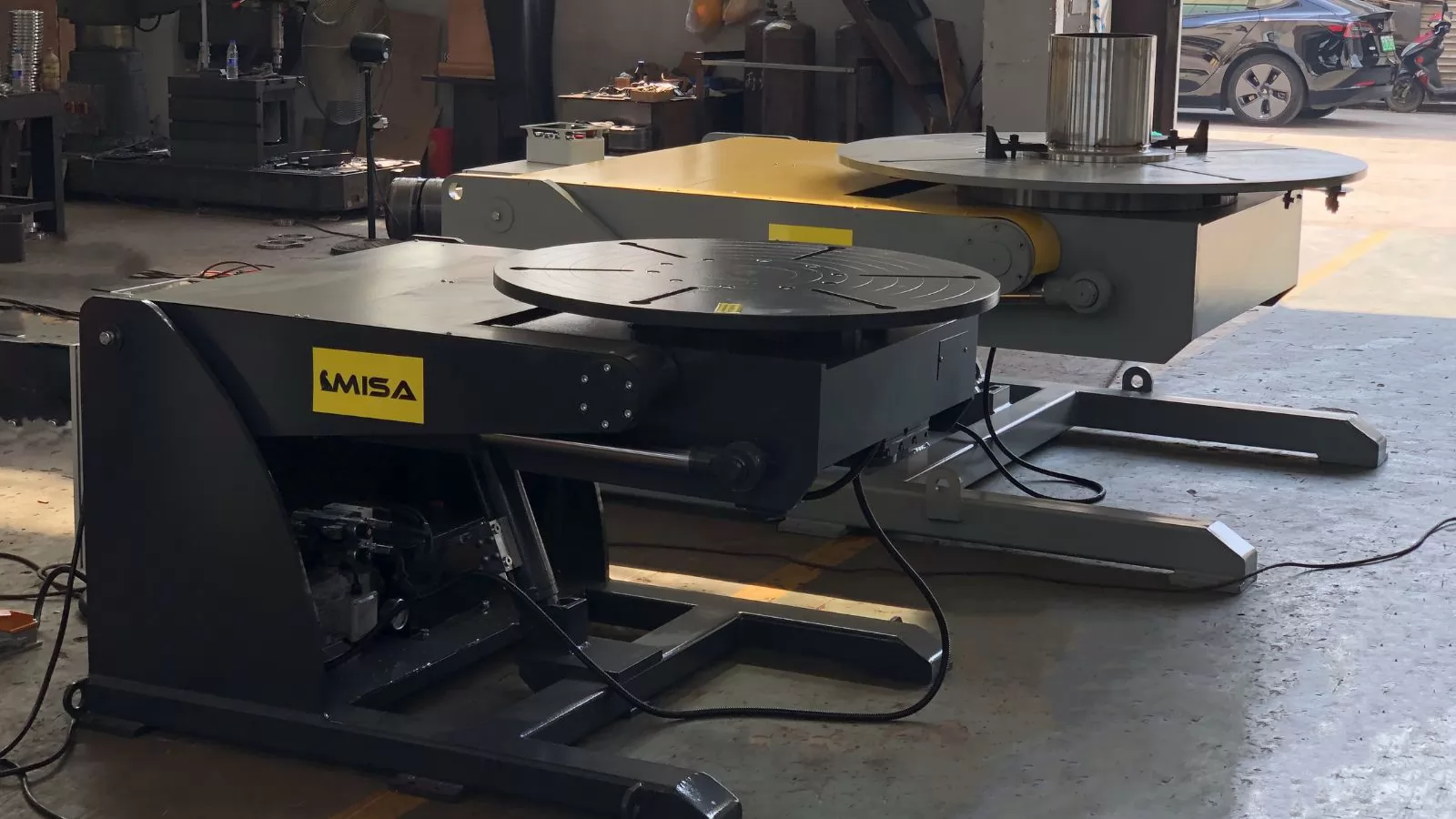
-
Structure: Combines rotation, tilt, and elevation (lift), providing enhanced spatial control for welding operations.
-
Best For: Projects requiring variable height access like cylindrical tanks or pressure vessels.
-
Advantages: Excellent ergonomics for welders; increases welding precision and accessibility.
-
Limitations: Higher cost and larger footprint.
-
Industries Used: Oil & gas, chemical processing, heavy vessel fabrication.
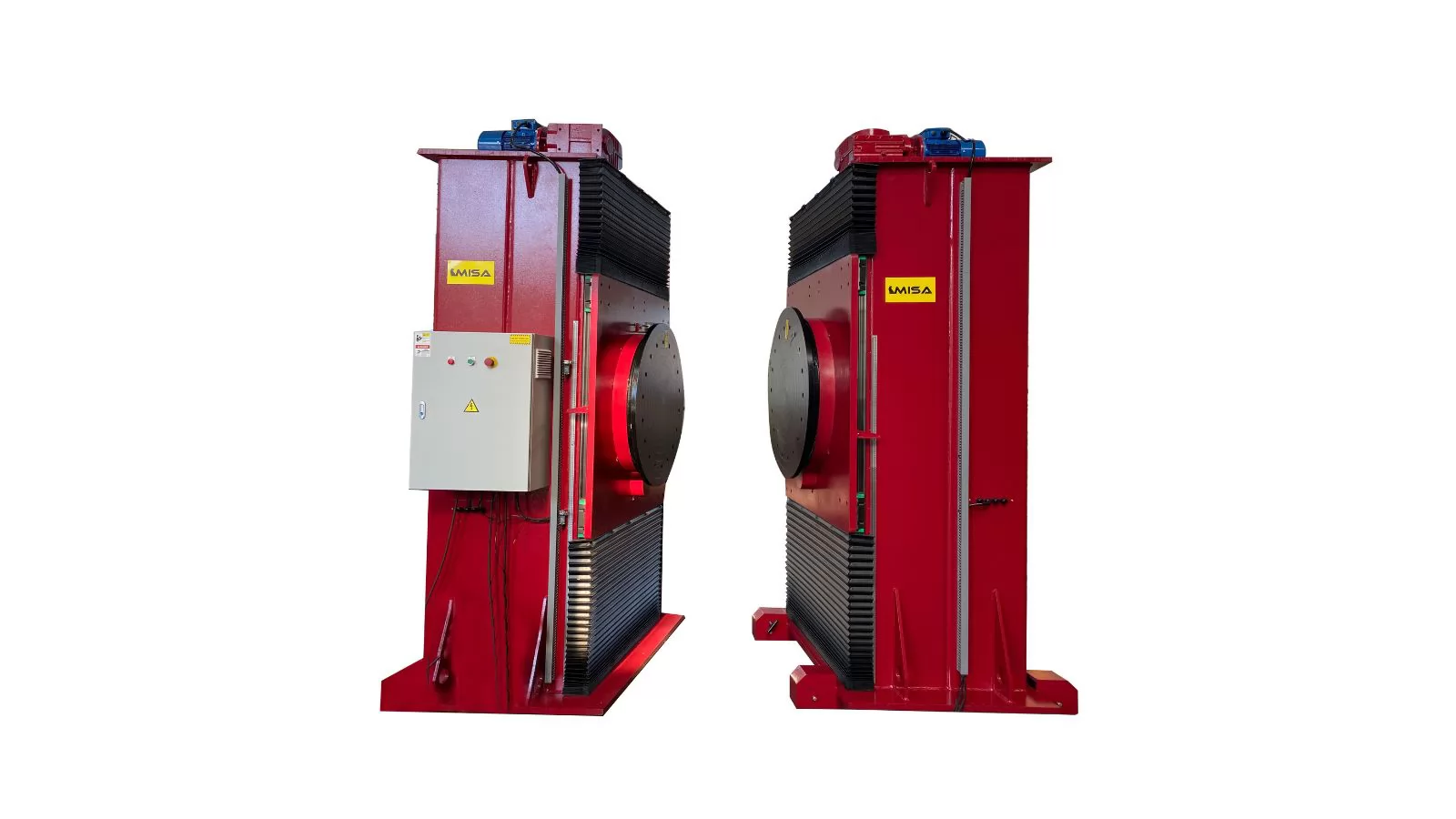
-
Structure: These positioners use a driven headstock and a free-spinning tailstock to hold long or tubular workpieces horizontally.
-
Best For: Shafts, pipes, and structural beams requiring full-length support.
-
Advantages: Ensures high stability for elongated parts; allows for even rotation.
-
Limitations: Requires precise alignment; not suitable for asymmetrical workpieces.
-
Industries Used: Automotive driveshaft manufacturing, aerospace, structural steel fabrication.
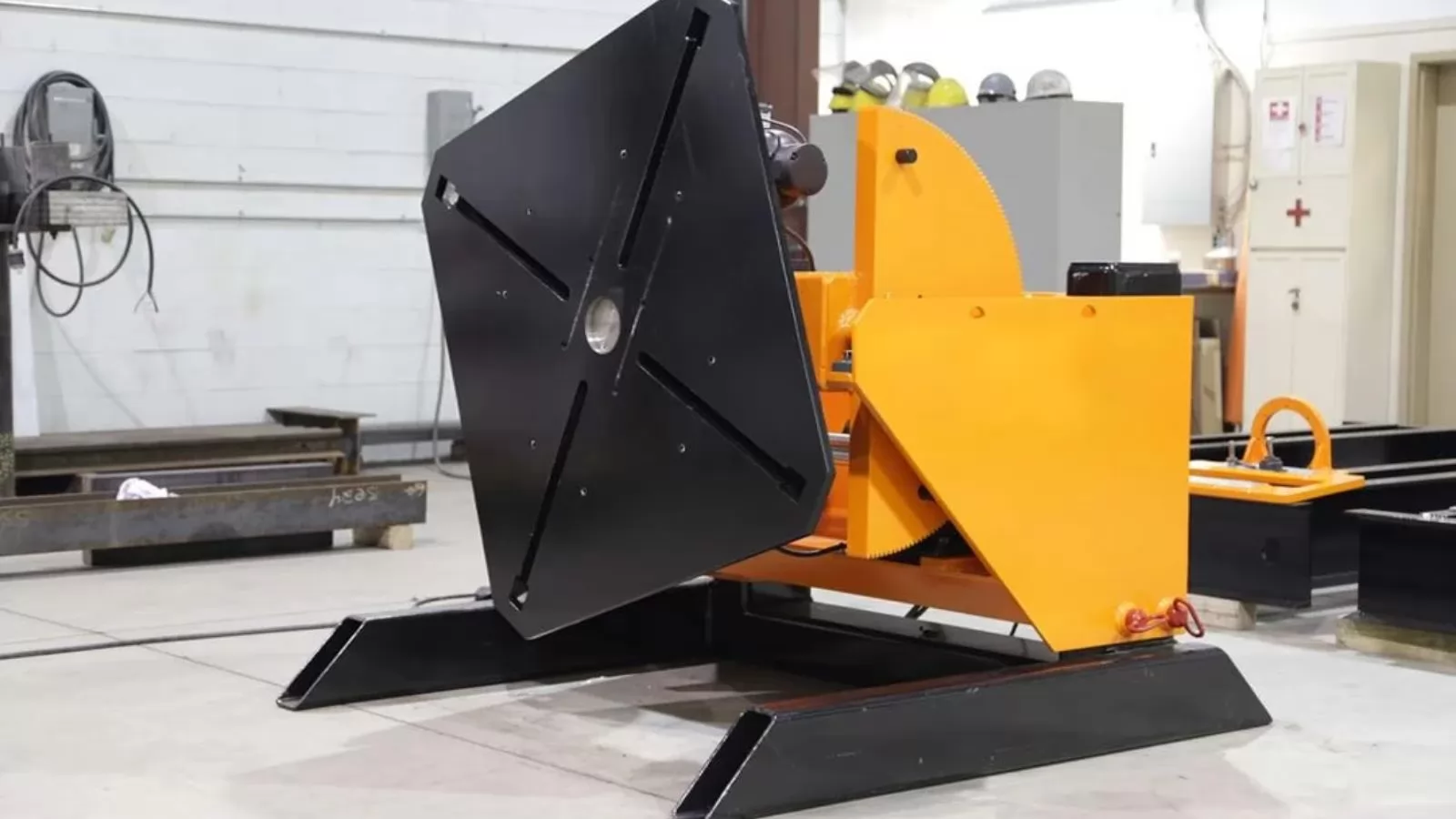
-
Structure: Offers synchronized tilting and rotating movement with adjustable speed control.
-
Best For: Complex welds that require multiple angles and axis changes during the process.
-
Advantages: Extremely versatile; allows near-complete access to all welding surfaces.
-
Limitations: Mechanical complexity; higher skill requirement for setup.
-
Industries Used: Aerospace, defense manufacturing, robotics integration.
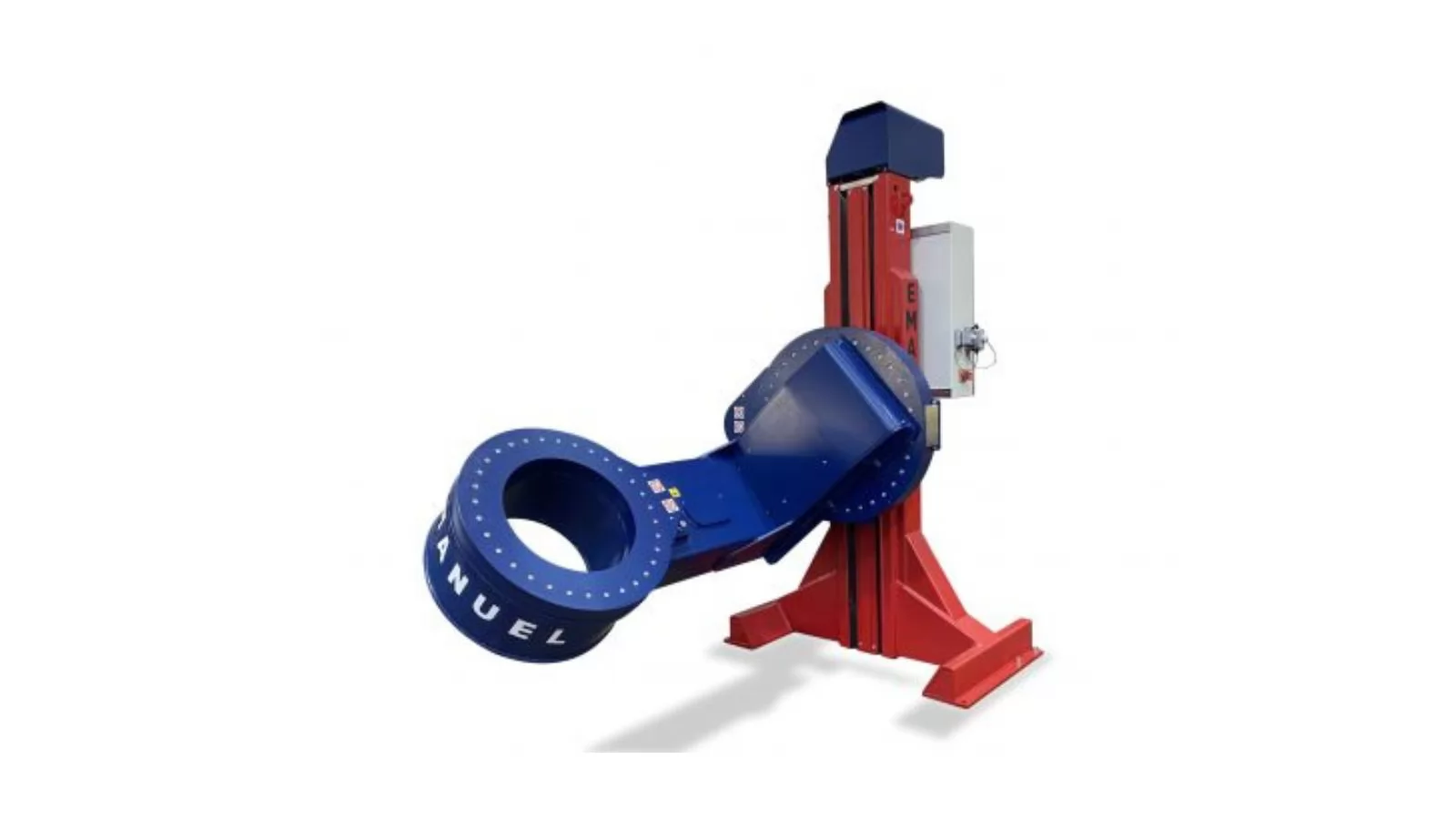
-
Structure: Skyhook systems allow a component to rotate in multiple planes with 360° access, often mounted vertically.
-
Best For: Irregularly shaped components needing multi-axis orientation.
-
Advantages: Provides superior maneuverability and operator access.
-
Limitations: Specialized use; higher cost; requires space and training.
-
Industries Used: Aircraft component fabrication, custom vehicle chassis welding.
-
Structure: Equipped with self-centering chucks or rollers for securely rotating cylindrical pipes during welding.
-
Best For: Pipe-to-pipe, pipe-to-flange, or pipe-to-fitting joints.
-
Advantages: Prevents distortion; ideal for circumferential welds.
-
Limitations: Limited to cylindrical shapes; requires precise clamping.
-
Industries Used: Oil pipelines, HVAC systems, plumbing prefabrication.
-
Structure: Heavy-duty machines that use industrial gear systems for controlled and powerful rotation.
-
Best For: Massive workpieces like pressure vessels, boilers, or ship parts.
-
Advantages: High torque; stable and reliable for heavy materials.
-
Limitations: Less flexibility; bulkier units.
-
Industries Used: Shipbuilding, power plant fabrication, structural steelworks.
-
Structure: Operated manually by levers or hand wheels without motorization.
-
Best For: Lightweight parts and occasional welding tasks.
-
Advantages: Affordable, compact, and simple to operate.
-
Limitations: No automation; dependent on operator skill.
-
Industries Used: Hobby welding, educational use, small-scale workshops.
-
Structure: Utilizes hydraulic power for tilting and rotation to handle heavy or off-center loads smoothly.
-
Best For: Large, awkwardly balanced components.
-
Advantages: Smooth, precise movement; high load capacity.
-
Limitations: Higher maintenance; needs hydraulic system monitoring.
-
Industries Used: Mining machinery, pressure tank manufacturing, industrial automation.
-
Structure: Integrated motors control rotation and tilt with speed adjustability.
-
Best For: Medium to high-volume production requiring repetitive welds.
-
Advantages: Increases throughput; allows for programmable operations.
-
Limitations: Costlier than manual models; requires electrical setup.
-
Industries Used: Automotive assembly, medium fabrication, consumer goods welding.
-
Structure: Lightweight, mobile units that can be transported to different job sites or welding stations.
-
Best For: On-site or field welding operations.
-
Advantages: Compact, easy to deploy, ideal for hard-to-reach locations.
-
Limitations: Smaller load capacity; limited movement range.
-
Industries Used: Construction sites, repair services, mobile welding units.
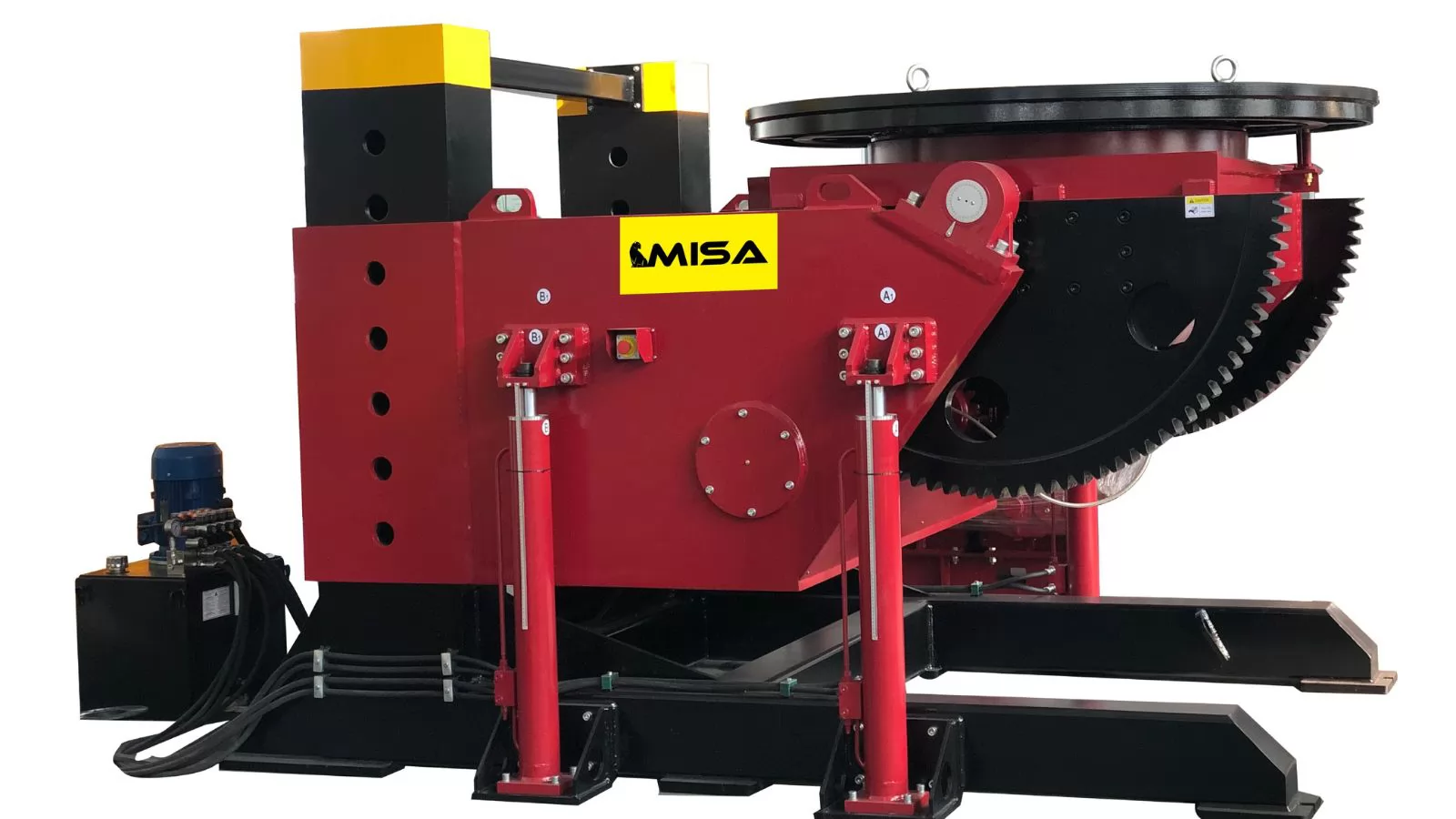
-
Structure: Features a rotating horizontal platform or disc to perform circular or radial welding.
-
Best For: Round plates, rings, and flat circular components.
-
Advantages: Smooth rotation; excellent for flat seam welds.
-
Limitations: Tilt or elevation not included in basic models.
-
Industries Used: Food processing machinery, automotive parts, electrical enclosures.
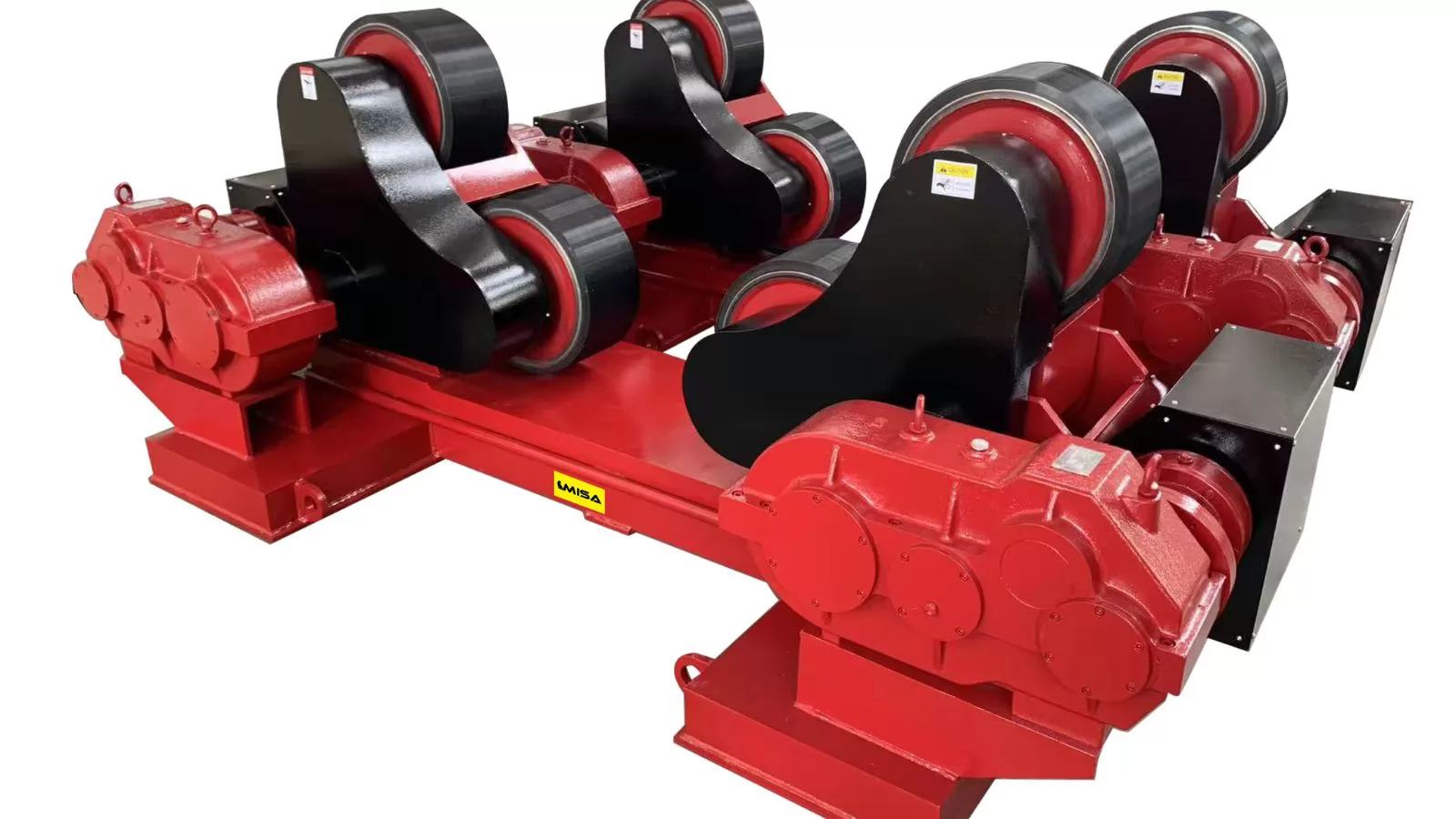
-
Structure: Uses rollers to support and rotate cylindrical tanks or pipes.
-
Best For: Long, heavy cylinders or tanks that need longitudinal welding.
-
Advantages: Allows continuous welding without repositioning; supports extreme weights.
-
Limitations: Only supports round, symmetrical parts.
-
Industries Used: Storage tank fabrication, oil & gas sector, wind turbine towers.
-
Structure: Synchronized with robotic welding arms, enabling automated and precise welds.
-
Best For: Fully automated welding lines or high-precision jobs.
-
Advantages: Reduces human error; increases consistency; ideal for mass production.
-
Limitations: High setup cost; requires integration expertise.
-
Industries Used: Automotive, electronics, aerospace manufacturing.
-
Structure: Engineered from scratch or modified based on specific client or project needs.
-
Best For: Unconventional components, prototype systems, or strict compliance standards.
-
Advantages: Tailored functionality; built to exact specs.
-
Limitations: Longer lead time; higher upfront cost.
-
Industries Used: R&D centers, bespoke machinery, government defense contracts.
Choosing the right welding positioner can dramatically influence both the efficiency and the quality of your welding operations. Here are the key factors to consider:
Load Capacity
-
The positioner's load capacity must match or exceed the weight of your heaviest workpiece.
-
Exceeding the recommended load could cause equipment failure, poor performance, or even serious accidents.
-
Tip: Always include a 20-30% safety margin above your maximum expected load.
Rotation Speed
-
Different welding applications demand different rotation speeds.
-
High-speed rotation is ideal for thin materials and small weld beads, while slow, powerful rotation is better for heavy-duty welding.
-
Variable Speed Control: Ensure the positioner offers adjustable speed settings for maximum flexibility.
Tilt Range
-
Tilt angles typically range from 0° to 135°, depending on the model.
-
A greater tilt range allows for better positioning of complex welds and reduces the need for manual repositioning.
-
Consider multi-axis models if your projects require extreme tilting.
-
Manual Controls: Cheaper and simpler but require operator expertise.
-
Remote Controls: Improve convenience and safety.
-
Programmable Logic Controllers (PLC): Ideal for automated and repetitive tasks.
-
Choosing the right control interface ensures smoother operation and reduces operator fatigue.
Safety Features
-
Look for essential safety elements such as:
-
Emergency stop buttons
-
Overload protection systems
-
Non-slip surfaces
-
Locking mechanisms
-
Safety should never be compromised, especially when dealing with heavy, rotating equipment.
Welding positioners are indispensable across a variety of industries due to their ability to improve productivity and weld quality. Here’s where they’re most commonly used:
Aerospace
In aerospace manufacturing, precision is non-negotiable. Positioners ensure aircraft components like turbines, fuselage frames, and landing gears are welded with absolute accuracy.
Automotive
Mass production lines in automotive plants use robotic and manual positioners to weld frames, axles, and exhaust systems efficiently and consistently.
Oil and Gas
Pipelines, pressure vessels, and offshore drilling components demand welding with tight quality controls, making pipe and roller positioners critical.
Heavy Equipment Manufacturing
For building excavators, bulldozers, and cranes, heavy-duty gear-driven positioners handle enormous, oddly shaped parts with ease.
Shipbuilding
Shipyard welding involves huge metal sections that must be rotated and tilted accurately. Positioners simplify these tasks and reduce manual handling risks.
Keeping your welding positioners in top shape maximizes their lifespan and ensures consistent performance.
Routine Inspection Checklist
Check for unusual vibrations or noises during operation. Inspect gearboxes and bearings for wear.Ensure all safety systems are functioning properly.
Lubrication and Cleaning
Regularly lubricate moving parts as per the manufacturer’s schedule. Keep control panels and electrical components clean and dry.
Troubleshooting Common Issues
-
Problem: Jerky rotation → Solution: Check gear lubrication.
-
Problem: Overheating motors → Solution: Verify ventilation and load limits.
-
Problem: Tilt malfunctions → Solution: Inspect hydraulic systems or actuators.
Safety is paramount when working with welding positioners due to the combination of heavy materials, high temperatures, and mechanical movements.
Pre-Operation Safety Checks
Before beginning any welding job:
-
Inspect Load Limits: Ensure the workpiece does not exceed the rated capacity.
-
Secure Workpieces: Double-check that clamps, chucks, and rollers are tightly secured.
-
Examine Electrical Connections: Look for loose wires or worn insulation.
Handling Heavy Loads
When managing large or heavy parts:
-
Use cranes or hoists to load/unload materials safely.
-
Never stand directly beneath suspended loads.
-
Center the workpiece to avoid imbalance during rotation.
Emergency Shutdown Procedures
Operators must be trained to:
-
Locate and use emergency stop buttons immediately.
-
Respond quickly to abnormal noises, jerky movements, or equipment overheating.
-
Safely power down the system and report malfunctions without attempting DIY repairs.
Custom-built welding positioners allow manufacturers to tailor equipment to unique project specifications.
Tailored Design Options
Customizations include:
-
Special jaw designs for irregular parts
-
Multi-axis programmable movements
-
Oversized or ultra-heavy load capacities
Add-Ons and Accessories
Enhancements may involve:
-
Remote control panels
-
Motorized clamps and fixtures
-
Integrated cooling systems for high-heat operations
-
Position sensors and feedback loops for real-time adjustments
Working with Manufacturers
For optimal customization:
-
Provide detailed CAD drawings or 3D models of your workpieces.
-
Clarify operational needs like load variance, speed requirements, and safety standards.
-
Discuss future-proofing options such as modular expansion capability.
1. What is the best welding positioner for beginners?
For beginners, a 2-axis manual welding positioner is ideal due to its simplicity, affordability, and ease of operation.
2. How much weight can a typical welding positioner hold?
Load capacities vary widely. Small positioners handle 100–500 pounds, while heavy-duty models can support up to 100,000 pounds or more.
3. Can I automate my existing manual welding positioner?
Yes, many manufacturers offer upgrade kits to motorize manual positioners, allowing for variable speed and remote control capabilities.
4. What industries benefit most from welding positioners?
Industries such as aerospace, automotive, oil and gas, shipbuilding, and heavy machinery manufacturing see significant benefits from welding positioners.
5. How do I maintain my welding positioner?
Routine maintenance includes lubrication, inspection of mechanical components, electrical system checks, and ensuring software updates if applicable.
6. Are customized welding positioners expensive?
While they cost more upfront, custom-built positioners often offer a faster ROI due to improved productivity, reduced errors, and tailored efficiency.
Welding positioners are vital tools that enhance the efficiency, safety, and quality of welding operations across a vast range of industries. Understanding the different types of welding positioners, their applications, and how to choose the right one ensures optimal performance for any project size or complexity.
By investing in the appropriate equipment and maintaining it properly, manufacturers can achieve higher precision, faster production times, and superior weld quality — keeping them competitive in today's demanding market.
Whether you're a small workshop or a multinational corporation, choosing the right welding positioner is a strategic decision that delivers measurable returns.